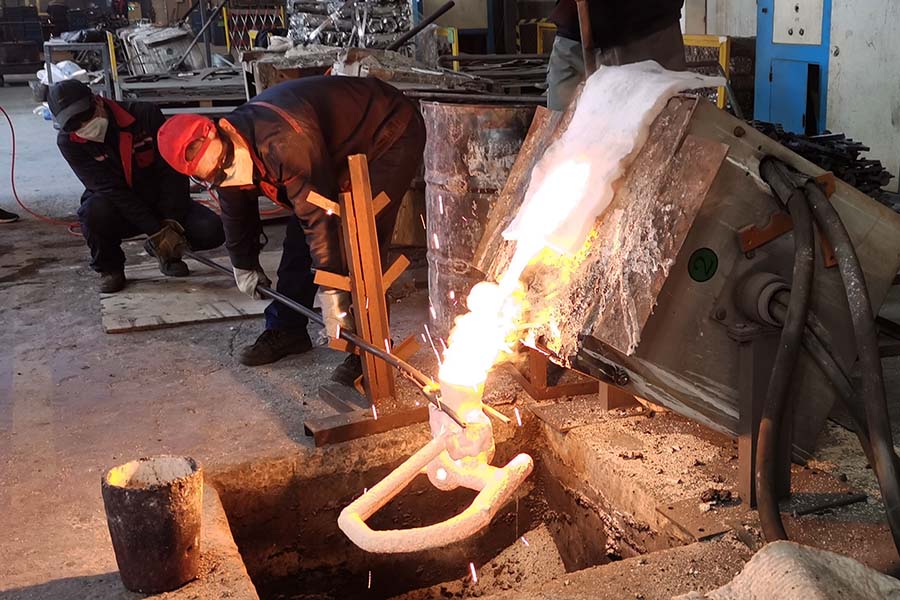
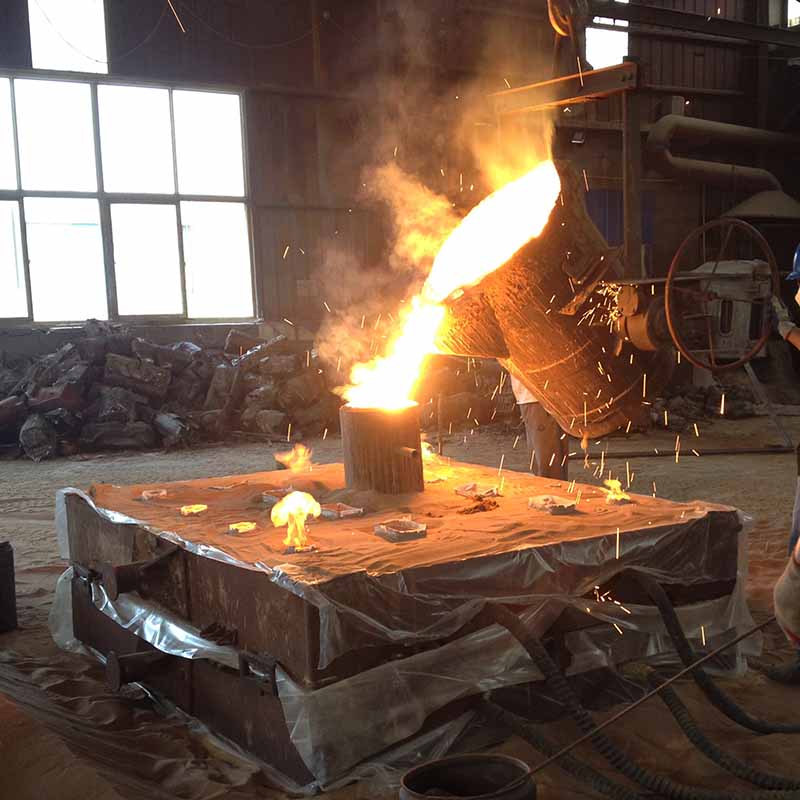
Леенето е един от най-ранните методи за формоване на метал, познат на хората. Това обикновено означава изливане на разтопен метал в огнеупорна форма с кухина с формата, която трябва да се направи, и оставянето му да се втвърди. КогаВтвърден, желаният метален предмет се изважда от огнеупорната форма или чрез счупване на формата, или чрез разглобяване на формата. Втвърденият обект се нарича отливка. Този процес се нарича също леене и се нарича модерната фабрика, която се фокусира върху леене на метални частилеярна.
1. История на процеса на леене
Процесът на леене вероятно е открит около 3500 г. пр.н.е. в Месопотамия. В много части на света през този период медните брадви и други плоски предмети се изработват в отворени форми, направени от камък или изпечениглина. Тези форми бяха по същество от едно парче. Но в по-късни периоди, когато е било необходимо да се правят кръгли предмети, такива форми са били разделяни на две или повече части, за да се улесни изваждането на кръглите предметиБронзовата епоха (около 2000 г. пр. н. е.) донесе много повече усъвършенстване на процеса на леене. Може би за първи път е изобретена сърцевина за правене на кухи джобове в предметите. Тези ядра са направени от печена глина.Също така, процесът на cire perdue или загуба на восък се използва широко за направата на орнаменти и фина работа.
Технологията на леене е значително подобрена от китайците от около 1500 г. пр.н.е. Преди това няма доказателства за каквато и да е леярска дейност, открита в Китай. Не изглежда да са били страхотнизапознат с процеса cire perdue, нито го е използвал широко, но вместо това се е специализирал в многокомпонентни форми за извършване на изключително сложни задачи. Те прекараха много време в усъвършенстване на матрицата до последния детайл, така че едва линеобходима е довършителна работа по отливката, направена от калъпите. Вероятно са правили форми за парчета, съдържащи внимателно монтирани части, наброяващи тридесет или повече. Всъщност много такива форми са били откритипровеждане на археологически разкопки в различни части на Китай.
Цивилизацията на долината на Инд е известна и с широкото си използване на отливане на мед и бронз за орнаменти, оръжия, инструменти и прибори. Но нямаше много подобрения в технологията. От вариПредмети и фигурки, които са били изкопани от местата в долината на Инд, те изглежда са били запознати с всички известни методи за отливане като отворена форма, матрица на парчета и процесът cire perdue.
Въпреки че на Индия може да се припише изобретяването на тигелната стомана, в Индия не е очевидно много от леенето на желязо. Има доказателства, че производството на желязо е започнало около 1000 г. пр.н.е. в Сирия и Персия. Появява сечечугунолеенетехнологията в Индия се използва от времето на нашествието на Александър Велики, около 300 г. пр.н.е.
Известният железен стълб, който в момента се намира близо до минара Кутб в Делхи, е пример за металургичните умения на древните индианци. Дълъг е 7,2 м и е изработен от чисто ковко желязо. Предполага се, че това е отпериод на Чандрагупта II (375-413 г. сл. Хр.) от династията Гупта. Степента на ръждясване на този стълб, който стои отвън на открито, е практически нулева и дори вкопаната част ръждясва изключително бавно. товатрябва първо да е отлят и след това изкован до крайната форма.
2. Предимства и ограничения
Процесът на леене се използва широко в производството поради многото си предимства. Разтопеният материал се влива във всеки малък участък в кухината на матрицата и като такъв във всяка сложна форма – вътрешнаили външен – може да се направи с процеса на леене. Възможно е да се отлеят практически всякакви материали, независимо дали са черни или цветни метали. Освен това необходимите инструменти за леене на форми са много прости иевтино. В резултат на това, за пробно производство или производство на малка партида, това е идеален метод. Възможно е в процеса на леене количеството материал да се постави там, където е необходимо. В резултат на товаможе да се постигне намаляване на теглото в дизайна.Отливкиобикновено се охлаждат равномерно от всички страни и следователно се очаква да нямат насочени свойства. Има определени метали и сплавикоито могат да бъдат обработени само чрез леене, а не чрез друг процес като коване поради металургични съображения. Могат да се правят отливки с всякакви размери и тегло, дори до 200 тона.
Въпреки това, точността на размерите и повърхностното покритие се постигат от нормалнотопроцес на леене в пясъкне би било подходящо за окончателно приложение в много случаи. За да се вземат предвид тези случаи, някои специални кастингиса разработени процеси като леене под налягане, подробностите за които са дадени в следващите глави. Освен това процесът на леене в пясък е трудоемък до известна степен и затова много подобрения са насочени към него,като машинно формоване и леярска механизация. При някои материали често е трудно да се отстранят дефекти, произтичащи от наличната влагапясъчни отливки.
3. Условия за кастинг
В следващите глави ще се видят подробностите за леенето в пясък, което представлява основния процес на леене. Преди да навлезете в детайлите на процеса, ще бъде дефинирането на няколко речникови думи за кастингподходящо.
Колба– Колбата за формоване е тази, която държи пясъчната форма непокътната. В зависимост от позицията на колбата в структурата на матрицата, тя се нарича с различни имена като плъзгане, копче и буза. Изработена е от дървоза временни приложения или по-общо от метал за дългосрочна употреба.
Плъзнете– Долна формовъчна колба
Справи се– Горна формовъчна колба
Буза– Междинна колба за формоване, използвана при формоване на три части.
Модел– Моделът е реплика на крайния обект, който трябва да бъде направен с някои модификации. Кухината на формата се прави с помощта на шаблона.
Разделителна линия– Това е разделителната линия между двете формовъчни колби, които образуват пясъчната форма. При разделен модел това е и разделителната линия между двете половини на шаблона
Долен борд– Това е дъска, която обикновено се прави от дърво, която се използва в началото на производството на формата. Шарката първо се държи на долната дъска, върху нея се поръсва пясък и след това се трамбова в плъзгача.
Облицовъчен пясък– Малкото количество въглероден материал, поръсен върху вътрешната повърхност на формовъчната кухина, за да се даде по-добро покритие на повърхността на отливките
Формовъчен пясък– Това е прясно приготвеният огнеупорен материал, използван за направата на кухината на формата. Това е смес от силициева глина и влага в подходящи пропорции за постигане на желаните резултати и заобикаляшаблон, докато правите матрицата.
Поддържащ пясък– Това е, което съставлява по-голямата част от огнеупорния материал, намиращ се във формата. Състои се от използван и изгорен пясък.
Ядро– Използва се за направа на кухи кухини в отливки.
Басейн за изливане– Малка фуниевидна кухина в горната част на формата, в която се излива разтопеният метал.
Spure– Проходът, през който разтопеният метал от басейна за изливане достига до кухината на формата. В много случаи той контролира потока на метала в матрицата.
бегач– Проходите в разделителната равнина, през които се регулира потокът от разтопен метал, преди да достигне кухината на формата.
порта– Действителната входна точка, през която разтопеният метал влиза в кухината на формата.
Чаплет– Чаплетите се използват за поддържане на сърцевините вътре в кухината на формата, за да се погрижат за собственото си тегло и да преодолеят металостатичните сили.
Охладете се– Кокилите са метални предмети, които се поставят във формата, за да се увеличи скоростта на охлаждане на отливките, за да се осигури равномерна или желана скорост на охлаждане.
Щранг– Това е резервоар с разтопен метал, осигурен в отливката, така че горещ метал да може да тече обратно в кухината на формата, когато има намаляване на обема на метала поради втвърдяване
4. Процедура за изработване на пясъчна форма
Процедурата за изработване на типична пясъчна форма е описана в следните стъпки:
Първо, долната дъска се поставя или върху формовъчната платформа, или върху пода, което прави повърхността равна. Колбата за плъзгане се държи обърната на долната дъска заедно с плъзгащата част нашаблон в центъра на колбата на дъската. Трябва да има достатъчно разстояние между шаблона и стените на колбата, което трябва да бъде от порядъка на 50 до 100 mm. Отгоре се поръсва сух облицовъчен пясъкдъската и шарката, за да осигурят нелепкав слой. Прясно приготвен пясък за формоване с необходимото качество сега се изсипва във влакното и върху шаблона до дебелина от 30 до 50 mm. Останалата част от драг колбата енапълно запълнена с резервния пясък и равномерно уплътнена за уплътняване на пясъка. Трамбоването на пясъка трябва да се извършва правилно, за да не се уплътнява твърде силно, което затруднява отделянето на газове,нито прекалено хлабав, така че калъпът да няма достатъчно здравина. След приключване на трамбовката излишният пясък в колбата се изстъргва напълно с помощта на плоска щанга до нивото на ръбовете на колбата.
Сега, с вентилационна жица, която е тел с диаметър от 1 до 2 мм със заострен край, се правят вентилационни отвори в плъзгача до пълната дълбочина на колбата, както и в шаблона, за да се улесни отстраняването на газовете по време на кастингвтвърдяване. Това завършва подготовката на драг.
Готовата колба за плъзгане сега се преобръща към долната дъска, разкривайки шаблона, както е показано на снимката. С помощта на мазилка краищата на пясъка около шаблона се поправят и половината от шаблона се поставя върхушаблона за плъзгане, като го подравнявате с помощта на щифтове. Колбата за справяне отгоре на плъзгача се намира отново подравнена с помощта на щифтовете. Сухият разделителен пясък се поръсва върху цялото влачене и върху шарката.
На малко разстояние от около 50 мм от шаблона се намира леников щифт за направата на лековия проход. Също така, щифтът на щранга, ако е необходимо, се съхранява на подходящо място и прясно приготвен пясък за формоване, подобен на тозиот влака заедно с подложката се поръсва пясък. Пясъкът се трамбова старателно, излишният пясък се изстъргва и се правят вентилационни отвори навсякъде в дръжката, както при драг.
Лековият щифт и щифтът на щранга се изваждат внимателно от колбата. По-късно басейнът за изливане се изрязва близо до горната част на леяка. Кожухът е отделен от плъзгача и всякакъв насипен пясък върху интерфейса на кожуха и плъзгачаот влака се издухва с помощта на духало. Сега, половинките на капака и шаблона за влачене се изтеглят с помощта на изтеглящите шипове и натискане на шаблона навсякъде, за да се увеличи леко кухината на формата, така честените на формата не се развалят от изтеглящия се модел. Пътеките и портите се изрязват във формата внимателно, без да се разваля матрицата. Всеки излишен или насипен пясък, който се намира в каналите и кухината на формата, се издухвадалеч с помощта на духалото. Сега облицовъчният пясък под формата на паста се нанася върху цялата кухина на формата и плъзгачите, което би придало на готовата отливка добро покритие на повърхността.
Сърцевината от сух пясък се приготвя с помощта на кутия за сърцевина. След подходящо изпичане се поставя в кухината на формата, както е показано на снимката. Корпусът се заменя на плъзгача, като се грижи за подравняването на двете с помощта накарфици. Подходяща тежест се поддържа върху капака, за да се грижи за насочената нагоре металостатична сила по време на изливането на разтопен метал. Сега формата, както е показано на снимката, е готова за изливане.
Време за публикуване: 25 декември 2020 г